PROCESSING APPLICATION
Hold tight! We’re comparing your resume to the job requirements…
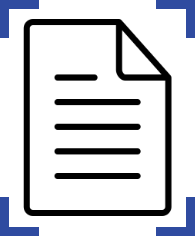
ARE YOU SURE YOU WANT TO APPLY TO THIS JOB?
Based on your Resume, it doesn't look like you meet the requirements from the employer. You can still apply if you think you’re a fit.
Job Requirements of Production Lead:
-
Employment Type:
Full-Time
-
Education:
High School
-
Location:
Kansas City, MO (Onsite)
Do you meet the requirements for this job?
Production Lead
Primary Purpose
The Team Lead serves as a support resource, leading team members to meet production schedules, facilitate the safe and productive manufacture of high quality products, effectively drive and maintain the standardized work process; train team members in the proper method; and help the team to succeed in an environment based on BOS, continuous improvement, Lean manufacturing, and 5-S. Key characteristics of a successful team leader are problem-solving, coaching and eliminating waste in the organization by responding to abnormalities and following the TMS philosophy.
Duties
Safety:
- Review the safety board with all team members daily.
- Create a mentally-engaged, physical, and professional safe environment.
- Champion and promote the plant’s safety policies and procedures by adopting the Tenneco safety culture.
- Lead by example in promoting safety practices and policies, including but not limited to, initiating start-of -shift stretches, wearing proper PPE, and holding all team members accountable for wearing theirs; following LOTO procedures; reminding the team about the importance of Hazcom labels (present, correct and legible data) and MSDS information.
- Report team member injuries and/or illnesses to Group Leader.
Ergonomics:
- Observe team members’ techniques as they perform the job functions and reduce overburden by counter measuring any awkward or excessive movements. Collaborate with the supervisor and/or EH&S Manager to continuously improve the ergonomics of the work.
5-S Process:
- Daily promote the 5-S Process for the cell or department.
- Continually evaluate the 5-S condition by observing the process area and follow–up on abnormalities.
- Complete any 5-S documentation and records as required by the 5-S plan.
Standardized Work:
- Team Leaders or their assigned designee train the team members in Standardized Work practices and follow up on any concerns that arise, actively listening for team members’ techniques or methods that potentially improve the standardized work.
- Lead by example to ensure consistency of standardized work by all team members.
- Coordinate the “continuous improvement” of Standardized Work and follow-up to ensure changes are made or abnormalities are resolved.
- Train and audit team members in standardized work, update and revise standardized work (as necessary), and complete the training matrix to document all training.
Job Instruction Training:
- Train using the standardized work Teaching methodology: 1) Prepare the team member; 2) Present the operation to the team member; 3) Allow the team member to try out the operation; and 4) provide coaching and follow up.
- Validate job breakdown sheets and standardize work processes with the team.
- Provide department/new hire orientation as required for replacements.
Communication:
- Communicate with the next shift any and all issues/concerns resulting from your shift’s operations.
- Provide timely and effective feedback to help team members to strengthen specific skill areas needed to accomplish a task or solve a problem.
- Discuss in Glass Walls information concerning safety, quality, inventory, production schedules, etc and fosters continuous improvement through communication.
- Listen and talk to the team members to get a better sense of their concerns and issues.
- Assure upward communication of the issues and/or successes of the cell on an as-needed basis.
- Maintain the glass wall in a neat and organized manner.
- Complete required paper work such as production record charts, quality information and logbook for shift-to-shift communication.
Production Output:
- Monitor the hourly production board to keep abreast of the current production rate
- Respond as primary support to team member calls when needed and to avoid a line stop.
Cell Operations (Product, Equipment, Quality):
- Confirm quality of materials and finished goods.
- Respond immediately when product abnormalities occur, solve the problem or report upward.
- Ensure set-up and operation of equipment in accordance with production requirements, procedures, and policies.
- Provide first response to line problems, document problems, resolve when possible, and follow up with resources to assure that the problem is corrected.
- Provide direction to team members to maintain compliance with process standards.
- Monitor and record efficiency and downtime for the area assigned to assure cell(s) are running to TAKT time.
- Continuously monitor and manage nonproductive time in the cell (changeover, downtime)
Defects & Scrap:
- Identify defects and suspect material and confer with the Group Leader to coordinate the appropriate disposition and elimination scrap
- Facilitate the proper completion of scrap documentation.
Operating Supplies:
- Monitor the usage of operating supplies.
Problem Solving / Philosophy:
- Lead actions to countermeasure a problem’s root cause, monitor the results and standardize the changes made to correct the problem.
- Be proactive in resolving problems in the cell, and elevate the need for assistance as necessary.
- “Go see” and observe problems firsthand, investigate and ensure an effective understanding of the facts/data.
- Solve problems utilizing the “scientific method.”
- Deepen process learning through rapid low-cost trials/experiments to solve problems.
Continuous Improvement:
- Lead and mentor the team to continuously improve their processes towards True North and strive to eliminate waste in the process.
Teamwork:
- Develop, support and monitor activities that foster teamwork within the group.
- Coordinate job assignments based on production needs and/or attendance concerns.
- Frequently analyze work balance to eliminate waste.
- Build strategic working relationships to achieve work and team goals.
- Support a positive work environment that is free of harassment, discrimination or other unlawful practices.
- Immediately report any unlawful or improper practices to their Group Leader and or Human Resources.
Daily Paperwork:
- Complete required paperwork such as quality scrap sheet and TKC control sheets.
Requirements
- Must possess knowledge to read, write, and perform basic math skills (includes basic algebra, fractions, geometry).
- Must have the ability to carry out instructions furnished in written, oral or diagram forms.
- The ability to operate, troubleshoot, make minor adjustments and/or perform preventive maintenance on metal bending, welding, forming, fabrication, and assembly equipment would be beneficial.
- Demonstrated experience in effective use of quality control gauges/equipment, inventory systems, blueprint interpretation, computer applications, and SPC charting where applicable.
- Ability to read and interpret documents such as safety rules, operating and maintenance instructions, and procedure manuals.
- Subject to the needs of the position and boundary area, obtain a valid forklift license, i.e. Shipping.
- Ability to write routine reports and correspondence. Ability to interact cooperatively and collaboratively with co-workers and supervision.
- Follow all changes, projects, and orders through to full completion.
- Must have good facilitation and decision-making skills.
- Ability to organize work under constant demands and changing priorities.
- Demonstrated ability to logically reason and apply the problem-solving process.
- Ability to communicate effectively verbally and in writing, manage multiple priorities, work effectively alone or in a team environment, adapt to changing work requirements, emulate strong interpersonal skills and effectively interact with people and motivate high performance of work team.
- Must demonstrate professional and ethical leadership.
- Must be willing to accept challenges and opportunities of acting in a leadership role and suggestions/recommendations for professional development.
- Strong basic math skills in calculations, tracking and analysis.
- Must possess a desire to champion change and the ability to motivate others to do so as well.
- Must have excellent attendance and punctuality and be in compliance and good standing with local Attendance Policy
- No Employee Warning notices for 3 months prior to application.
- Ability to work any shift as needed.
- Flexible enough to work long hours to meet customer needs from time to time.
Qualifications
- High school diploma or GED equivalent are required.
- Working knowledge of computer programs including Microsoft Office, Lotus Notes, and SAP preferred.
- Industrial or manufacturing experience with two (2) years shop floor operations experience preferred.
- Ability to effectively oversee shift operations in the absence of the Group Leader required.
The physical demands described here are representative of those that must be met by an employee to successfully perform the essential functions of this job. Reasonable accommodations may be made to enable individuals with disabilities to perform the essential functions.
- The employee is regularly required to stand in place for long periods of time and uses dexterity of hands to handle and feel materials.
- Ability to communicate effectively.
- The employee is occasionally required to sit, climb, or balance, stoop, kneel, crouch, or crawl.
- The employee must regularly lift and/or move up to 50 pounds, and may occasionally lift and/or move more weight with the safety assistance of another employee.
- Specific vision abilities required by this job include close vision, distance vision, peripheral vision, depth perception, and ability to adjust focus.
The work environment characteristics described here are representative of those an employee encounters while performing the essential functions of this job. Reasonable accommodations may be made to enable individuals with disabilities to perform the essential functions.
- Regular exposure to moving mechanical parts.
- Occasional exposure to fumes or airborne particles, liquids including oil, extreme heat, risk of electrical shock, and vibration.
- Noise levels in the work environment are usually loud, requiring hearing protection.
- Temperatures will vary in the factory including extreme heat or cold climate conditions.
- The work spaces will sometimes be somewhat crowded.
Need For Driving or Travel
On rare or infrequent occasions, the manager may assign a short trip to travel by automobile or commercial carrier to attend meetings, training, conferences, customer visits or other plants.