PROCESSING APPLICATION
Hold tight! We’re comparing your resume to the job requirements…
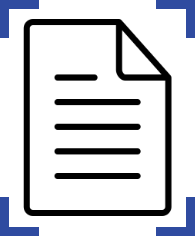
ARE YOU SURE YOU WANT TO APPLY TO THIS JOB?
Based on your Resume, it doesn't look like you meet the requirements from the employer. You can still apply if you think you’re a fit.
Job Requirements of Quality Manager:
-
Employment Type:
Full-Time
-
Experience:
7 years
-
Education:
4 Year Degree
-
Location:
Springdale, AR (Onsite)
Do you meet the requirements for this job?
Quality Manager
Arconic is currently in search of Quality Manager to join our Business and Construction Team in Springdale, Arkansas.
At Arconic, we are looking for people who share our values of integrity, inclusion, and diversity, and who demonstrate agility, results commitment, and the capability to grow themselves and others. In return, we offer the opportunity to Grow Together with ongoing opportunities for professional growth provided by a constantly changing environment, working alongside employees who value the people they work with just as much as the work they do.
Primary Responsibilities
- Developing and executing overall policy, strategy in extruded profiles stocks for construction products quality risk mitigations to ensure compliance with customer specifications and government regulations, continuous improvement in total customer satisfaction and manufacturing cost reduction.
- Utilize continuous improvement and operational excellence tools to drive business outcomes, included but not limited to A3’s, Hoshin Plans, Ishikawa diagrams, Visual Management Boards, Daily Management Activities and Quality operation metrics reviews/reporting.
- Management of all Quality functions for Quality Assurance Systems, Product Configuration, Process/Product Inspection, Test Lab Certification, Calibrations, and Manufacturing Operations, to include process engineering and growth/applications initiatives. Management of AS9100 system accreditation processes.
- Facilitate Quality focused kaizen events for departments based on the business needs to achieve immediate and sustainable improvements.
- Working with New Product Development and Innovation (NPD&I) production to determine quality requirements for new and existing products (aka Technical Inquiry Process). Establishing manufacturing plans and procedures to meet customer and internal requirements.
- Developing and challenging a team of highly motivated quality professionals to drive industry best in class. Developing succession plan and strategy working with Human Resources.
- Improve process control through the application of APQP (Advanced Product Quality Planning) methodologies.
Basic Qualifications:
- Bachelor of Science Degree in metallurgy, technology, engineering or related disciplines, advanced technical degree is preferred.
- Minimum of 7 years of work experience facilitating lean manufacturing programs.
- Minimum of 5 years supervisory experience, including the ability of developing a team, supervising, evaluating, training, and motivating employees, envisioning, and articulating the strategy, and passionately owning and driving the team towards achievement. Ability to work effectively with multiple facets management, operations, sale/marketing, technical, engineering personnel in a large matrix organization.
- Employees must be legally authorized to work in the United States. Verification of employment eligibility will be required at the time of hire. Visa sponsorship is not available for this position
Preferred Qualifications
- Masters Degree from an accredited institution
- ASQ, CQA, CQE, CQM, 6-sigma certifications desirable.
- Strong command and understanding in metallurgical practices in thermal-mechanical processing and heat treatment/pyrometry, material laboratory testing, nondestructive testing, statistical process control, FMEA’s, Control Plans, PPAP’s, system and special process audits etc.
- Demonstrated proficiency in structured and systematic problem solving, using factual, data driven, logical approaches. Able to research and analyze information of considerable difficulty and draw valid conclusions.
- Strong command of quality systems and leading change through strategic direction, as well as applicable customer specifications/requirements quality specifications, AS/EN/JISQ 9100, and ISO/IEC 17025 Quality Systems and Nadcap special processes requirements.
Arconic Corporation is a leading provider of aluminum sheet, plate and extrusions, as well as innovative architectural products, that advance the automotive, aerospace, commercial transportation, industrial and building and construction markets. Building on more than a century of innovation, Arconic helps to transform the way we fly, drive, and build. We are proud that 77% of our employees are happy working for Arconic and would recommend it as a great place to work and that 80% of our employees would recommend their managers to others.
We live our core values and commit to delivering sustainable value to our customers, our employees, our communities and our stakeholders.
At Arconic, we:
Act With Integrity.
We lead with respect, honesty, transparency and accountability.
Safeguard our Future.
We protect and improve the health and safety of our employees, communities and environment.
Grow Stronger Together.
We cultivate an inclusive and diverse culture that advocates for equity.
Earn Customer Loyalty.
We build customer partnerships through best-in-class products and service.
Drive Operational Excellence.
We pursue continuous improvement through innovation, agility, people development and collaboration.
Create Value.
We achieve success by generating and growing value for our stakeholders.
United States Equal Employment Opportunity Statement
Arconic is an equal opportunity employer that is committed to inclusion and diversity. We take action to ensure equal opportunity for all applicants without regard to race, color, religion, sex, sexual orientation, gender identity, national origin, disability, Veteran status, or other legally protected characteristics.