PROCESSING APPLICATION
Hold tight! We’re comparing your resume to the job requirements…
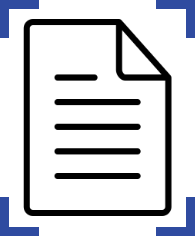
ARE YOU SURE YOU WANT TO APPLY TO THIS JOB?
Based on your Resume, it doesn't look like you meet the requirements from the employer. You can still apply if you think you’re a fit.
Job Requirements of EH&S or H&S Engineer:
-
Employment Type:
Full-Time
-
Location:
Waupun, WI (Onsite)
Do you meet the requirements for this job?
EH&S or H&S Engineer
'Own Your Career' supports Tenneco’s People Model, ensuring that we both “Select the Best” and “Build & Develop” internal talent.
It is our commitment to develop and promote great talent within the Tenneco team.
SUMMARY: Ensures compliance with applicable codes, and all environmental regulations as well as best practices are met and /or exceeded. Promotes the maintenance of a environmentally, healthy, safe and accident free work environment. Carries out these responsibilities in accordance with the organization's policies and applicable laws by performing the following duties personally or with the assistance of available internal or external resources
ESSENTIAL DUTIES AND RESPONSIBILITIES
- Responsible for working safely, adhering to the facility’s environmental, health and safety policies and procedures and continually monitoring the work environment to identify and communicate to supervisor / manager current or potential environmental, health or safety concerns.
- Responsible for the maintenance of the Health, Safety and Environmental Management Program as specified by the management systems and technical specifications.
- Oversees the administration of federal, state and local environmental regulatory requirements and complies with Corporate Environmental Health and Safety policies and procedures.
- Formulates general environmental, health and safety policies and procedures to be followed by company or plant personnel in compliance with local, state, and federal Occupational Safety and Health Administration (OSHA) rules and regulations.
- Inspects or tours organization facilities to detect existing or potential accident, ill health and environmental hazards, and recommends and implements corrective or preventative measures where indicated. Utilizes Continuous Ongoing Improvement projects (COI’s).
- Maintain compliance with Monitoring and Measurements and Legal and other requirements that we subscribe to for Environmental, Health and Safety requirements and reporting. Responsible for maintaining compliance to all state and federal regulations, rules and codes.
- Responsible for the EH&S Risk Assessments for all processes, equipment and the identification and controls of the Environmental Aspects and Impacts that will impact our employees, and the community. Consults with all departments on design and use of equipment, shops, and fire prevention and health / safety program.
- New hire Environmental, Health and Safety Training, for all required programs and procedures and the facilitation of Safety Teams, Safety Toolbox meetings and the content for required refresher training.
- Follow up on safety, health and environmental issues for all shifts, includes work orders put into the system by employees for repairs made to equipment. Follow up on all near miss and spill reports and the implantation of corrective actions.
- Review and update of lockout specific procedures for each piece of equipment in the facility and annual lockout performance audits.
- Maintains the Hearing Conservation Program which includes Annual Audiograms for all employees and Annual Noise survey.
- Responsible for the airborne and metal fluid testing for the facility.
- Responsible for the programs and the annual training for Emergency response, Hazardous Communications, Bloodborne Pathogens, First aid, CPR, Emergency preparedness and response plan, including all drills.
- Review of facility for confined spaces and entry of updates to program as required.
- Recertification of powered industrial truck drivers for employees and contractors.
- Respond for all mandates issued by the Global Environmental, Health and Safety Manager and to all safety mandates as issued by corporate.
- Participate in all conference calls on Safety, and any follow up as required.
- Achieve corporate targets and objectives for EHS and establish internal goals.
- Subcontractor and Contractor environmental, health and safety training and assessments.
- Machine assessments for new release, repair and rebuilt equipment and conduct annual machine assessments on facility equipment. Review layouts, plant movement of equipment and process changes for environmental, health and safety issues.
- Order and the maintenance of first aid kids, first responder kits, eyewash stations, fire blankets and any other supplies related to environmental, health and safety.
- Keeps managers and employees alert to environmental, health and safety hazards such as working with toxic fumes, dangerous chemicals, hazardous substances, unsafe equipment, or any condition that may cause ill health or injury.
- Responsible for ergonomic solutions for the facility employees.
- Responsible for the maintenance and documentation of programs and procedures for Environmental Health and Safety Management Systems.
- Compiles data and analyzes past and current year safety/EHS requirements to assist in preparation of annual budget and to justify funds requested.
- Confers with vendors to determine specifications and arrange for purchase of equipment, materials, or parts, and evaluates products according to specifications for environmental, health, safety and quality standards.
- Ability to read and interpret engineering blueprints, drawings, models, and other specifications to obtain data.
- Prepares graphs or charts of data or enters data into computer for analysis. Prepares reports and memorandums.
- Conduct FM-Tips for environmental, safety and health incidents and follow-up and verification on all corrective and preventative actions.
- Maintains the OSHA documentation and recordkeeping for the 300 log. Records all safety incidents from supervisor log and required environmental data into the Global EHS Reporting Portal.
- Participates in External Audits and carries out assigned internal audits, following through on non-compliance relating to those audits for the Environmental, Health and Safety Management System with the completion of corrective actions from audit findings.
- A knowledge of 5S principles and systems.
- Support and implement 5S principles and practice
- Daily attendance and update in a management metrics meeting
- All other responsibilities as assigned
- Must be able to work independently.
QUALIFICATION REQUIREMENTS:
To perform this job successfully, an individual must be able to perform each essential duty satisfactorily. The requirements listed below are representative of the knowledge, skill, and/or ability required.
EDUCATION and/or EXPERIENCE:
Associate’s degree (A. A.) or equivalent from two-year College or technical school; or six months to one year related experience and/or training; or equivalent combination of education and experience in the field of environmental, health and safety.
LANGUAGE SKILLS:
Ability to read to read and write English. Ability to read and interpret documents such as safety rules, operating and maintenance instructions, and procedure manuals. Ability to write routine reports and correspondence. Ability to speak effectively before groups of customers or employees of organization. Ability to read and interpret documents such as blueprints.
MATHEMATICAL SKILLS:
Ability to work with mathematical concepts such as probability and statistical inference, and fundamentals of plane and solid geometry and trigonometry. Ability to apply concepts such as fractions, percentages, ratios, and proportions to practical situations.
REASONING ABILITY:
Ability to apply common sense understanding to carry out instructions furnished in written, oral, or diagram form. Ability to deal with problems involving several concrete variables in standardized situations. Ability to interpret a variety of instructions in written, oral, diagrams or schedule form.
OTHER SKILLS and ABILITIES;
Able to work independently and with other members of the Engineering Department and co-workers involved in the production process. Must have understanding of computer operations and relevant software. Familiarity with some statistical programs a plus.
PHYSICAL DEMANDS: The physical demands described here are representative of those that must be met by an employee to successfully perform the essential functions of this job.
While performing the duties of this job, the employee is regularly required to walk; use hands to finger, handle, or feel objects, tools, or controls; reach with hands and arms; and talk and hear. The employee frequently is required to stand. The employee is occasionally required to sit; climb or balance; and stoop, kneel, crouch, or crawl.
The employee must regularly lift and/or move up to 10 pounds, frequently lift and/or move up to 25 pounds, and occasionally lift and/or move up to 50 pounds. Specific vision abilities required by this job include close vision, distance vision, color vision, peripheral vision, depth perception, and the ability to adjust focus.
WORK ENVIRONMENT: The work environment characteristics described here are representative of those an employee encounters while performing the essential functions of this job.
While performing the duties of this job, the employee is frequently exposed to extreme heat. The employee occasionally works near moving mechanical parts and is occasionally exposed to fumes or airborne particles.
The noise level in the work environment is usually loud.
You are encouraged to 'Own Your Career' to maximize your development and reach your full potential!