PROCESSING APPLICATION
Hold tight! We’re comparing your resume to the job requirements…
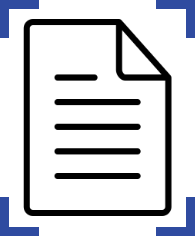
ARE YOU SURE YOU WANT TO APPLY TO THIS JOB?
Based on your Resume, it doesn't look like you meet the requirements from the employer. You can still apply if you think you’re a fit.
Job Requirements of Engineering Manager:
-
Employment Type:
Full-Time
-
Experience:
5 to 8 years
-
Education:
4 Year Degree
-
Location:
Manitowoc, WI (Onsite)
Do you meet the requirements for this job?
Engineering Manager
Tenneco is one of the world’s leading designer, manufacturers and marketers of automotive products for original equipment and aftermarket customers, with approximately 78.000 team members working at more than 300 sites worldwide. Through our four business groups, Motorparts, Ride Performance, Clean Air and Powertrain, Tenneco is driving advancements in global mobility by delivering technology solutions for diversified global markets, including light vehicle, commercial truck, off-highway, industrial, motorsport and the aftermarket.
JOB SCOPE:
Manage the Process Engineering Group (responsible for processing samples, quotes, new item introductions and Engineering changes) and also the Prototype Manufacturing Group (responsible for fabricating prototype and low volume production parts). Also manages the Quality team including the Plant Quality Manager (responsible for managing customer complaints, customer visit coordination, plant quality systems, etc)
JOB RESPONSIBILITIES:
- Responsible to collaborate with staff members to make plant level decisions.
- Supervise the process engineering team. Initiate, execute, and track team projects, improvement opportunities, and metrics.
- Direct and approve purchases of departmental supplies and equipment.
- Manufacturing Engineering Support for high level projects such as TS16949 implementation and other new manufacturing processes.
- Report to Plant Management on performance and improvement activities on a regular basis.
- Interface with Product and application Engineering, Sales and Marketing, and the customer.
- Provides a healthy and safe work place for employees by identifying and eliminating hazards
- Communicate and reinforce Quality Policy and Business Objectives and EHS rules and regulations
- Properly report, investigate, and implement corrective actions to quality problems and safety incidents.
- Targets to reduce customer concerns and external and internal PPM and to Eliminate, Reduce Reuse, or Recycle natural resources.
- Responsible for the implementation of new products and processes.
- Responsible for plant RFQ process
- Responsible for recognizing and implementing improvements to the manufacturing processes and products for increased productivity, improved quality, quicker response, reduced cost, and increased safety.
- Work with all departments in meeting customer expectations for quality, service, cost, and delivery.
- Works with Human Resources and Supervisors to resolve personnel related issues.
- Will conduct training as needed to support personnel and team development, problem resolution, and process improvements.
- Participates in the establishment and implementation of plant work rules, policies, and procedures and is responsible for the continued maintenance of the QS 9000 and ISO-14001 systems.
- Will participate with the local management staff to develop site goals and objectives and will be responsible for monitoring the progress and for ensuring the achievement.
- Prepares technical and analytical reports for management to monitor and make decisions regarding the plant’s operational performance and strategic planning.
- Administers other personnel functions.
- All other duties as assigned.
EDUCATION
- The ideal candidate will possess a bachelors degree in Manufacturing/Engineering/Business, or other related filed. Advanced degree preferred.
EXPERIENCE
- 5 - 8 years experience in manufacturing, engineering, materials, or quality management, preferably in an automotive supply environment.
- Must be a self-motivated team player, possessing excellent analytical and problem solving skills, including a working knowledge of production standards and measurement systems and possessing a proven record of cost savings and productivity gains.
- Must be proficient with Microsoft Office products, particularly the creation of production and capacity related spreadsheets and the summarization of information into easily read presentations.
- Must have excellent verbal and written skills. Must be able to effectively communicate with all levels of the organization and possess excellent human relations skills.
- Experience with Constraint Management, Lean Manufacturing, JIT, STOP, QS 9000 and ISO-14001 preferred.
- Detailed knowledge of manufacturing processes and capabilities.
- Ability to read and interpret documents such as safety rules, operating and maintenance instructions, and procedure manuals. Ability to write technical reports, business correspondence and procedures. Ability to effectively present information and respond to questions from groups of customers or employees.
- Analytical abilities necessary to troubleshoot complex manufacturing issues and processes.
- Interpersonal skills necessary to exchange information with variety of staff.
- Knowledge of applicable regulatory requirements, such as OSHA standards , TS16949 and ISO 14001 policies and procedures.
- Ability to establish and manage multiple priorities in a dynamic environment.
- Proven ability in a leadership role, guiding and directing a team towards a common goal; able to coach on leadership skills
- Knowledge of HR policies and procedures
- Proven ability to learn new concepts, processes, etc. quickly and utilize them within a team; ability to manage a large number of employees.
- Ability to create and communicate Process Failure Mode Effects Analysis (FMEA) and Control plans.
- Knowledgeable in FMTiPs.
- Able to access QMS documents and incorporate them into daily work activities.
- Able to access EHSMS standard procedures and work instructions and incorporates them into daily work activities.
- Financially savvy; understand the drivers of manufacturing costs; previous experience in efficiency improvements.
- Demonstrated ability to lead and motivate a team. Excellent relationship building skills.
- Strong written and verbal communication skills including the ability to communicate with all levels of management and hourly employees
- Good interpersonal skills, including tact and diplomacy, are necessary to supervise employees in a fair and consistent manner
- Must be able to counsel, guide and evaluate the work of others in a manner that motivates the achievement of company goals
- Must be able to maintain confidentiality of information
- Must have working knowledge of SPC
- Must be willing to travel
PHYSICAL AND MENTAL DEMANDS
To perform this job successfully, an individual must be able to perform each essential duty satisfactorily. The requirements listed below are representative of the knowledge, skill, and/or ability required. Reasonable accommodations may be made to enable individuals with disabilities to perform the essential functions.
- Must be able to make occasional trips to manufacturing sites and customers by air and by automobile.
- Able to be on call 24/7 for customer and manufacturing sites
- Able and willing to work around chemicals, coolants, oils, moving equipment, and electrical power.
- Ability to sit for an extended period of time (2 or more hours).
- Ability to clearly give and receive information through verbal (speaking & hearing) and written forms.
- Ability to closely examine and visually inspect parts and data.
- Ability to walk and move about, stoop and bend, and climb (ascend and descend) ladders.
- Works in all areas of the plant where dust, noise, and odors typical of the manufacturing environment exist.
We are committed to the safety and health of our employees. We adhere to social distancing recommendations and other protocols, ensuring a safe work environment for all.