PROCESSING APPLICATION
Hold tight! We’re comparing your resume to the job requirements…
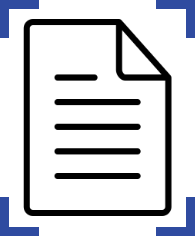
ARE YOU SURE YOU WANT TO APPLY TO THIS JOB?
Based on your Resume, it doesn't look like you meet the requirements from the employer. You can still apply if you think you’re a fit.
Job Requirements of Manufacturing Engineering Manager:
-
Employment Type:
Full-Time
-
Location:
Napoleon, OH (Onsite)
Do you meet the requirements for this job?
Manufacturing Engineering Manager
Tenneco is one of the world’s leading designer, manufacturers and marketers of automotive products for original equipment and aftermarket customers, with approximately 78.000 team members working at more than 300 sites worldwide. Through our four business groups, Motorparts, Ride Performance, Clean Air and Powertrain, Tenneco is driving advancements in global mobility by delivering technology solutions for diversified global markets, including light vehicle, commercial truck, off-highway, industrial, motorsport and the aftermarket.
Job Description
The incumbent will manage the team responsible for environmental, health, and safety leadership for the site. Individual is accountable for: directing EHS activities at his/her location(s); establishing EHS objectives and targets; internal reporting of EHS performance; communication of national, area, and local regulatory requirements, and; ensuring documents are available in the local languages. Position is responsible for: maintaining site ISO certifications (as applicable); assuring accurate and complete EHS reporting of metrics; assuring closure of company and regulatory agency findings on a timely basis; completion of required training for EHS personnel; managing interfaces with the public and governmental authorities with adverse findings and enforcement actions; directing actions during crises; creating a strong EHS culture that engages employees throughout the site in EHS teams and processes.
ESSENTIALS DUTIES AND RESPONSIBILITIES:
- Manages and directs site in achieving EHS targets & objectives. Directs development, maintenance, and achievement of goals in support of corporate and division EHS strategic initiatives.
- Facilitates risk assessment at the location to identify critical EHS hazards and aspects. Works with leadership team to create targets and objectives based on key EHS risks.
- Determines appropriate leading and lagging indicators to track performance against targets and objectives.
- Supports creation of EHS goals for the site manager and appropriate activity based goals for the leadership team, functional managers, and front-line supervisors to drive EHS culture, compliance, and results.
- Works to assign EHS element champions and facilitate their engagement in ownership of the EHS elements.
- Drives and promotes zero incident EHS culture throughout site.
- Creates and facilitates EHS engagement through EHS teams and committees needed to accomplish the established targets and objectives for the year.
- Works with leadership team and EHS element champions to complete an annual evaluation of compliance for EHS country, state, and local regulations.
- Pursues third party recognition for programs that establish the site EHS program as world class.
- Uses established EHS data processes to manage data such as injuries and illnesses, environmental metrics, risk assessments, EHS action items and other pertinent information.
- Create training matrices to ensure that all training is defined and tracked to completion
- Work with site leadership team and facilities to ensure that all key EHS operational controls are in place, on a PM program, and that EHS action items are resolved on a timely basis.
- Supporting Workers Compensation investigations in coordination with site HR.
In Addition to the regular duties of the highest ranking EHS person at site, the following responsibilities are assumed for that person, or designee:
- PPI – The EHS Coordinator, as appropriate, is the Plant Pollution Index Coordinator that is provided the authority by the Plant Manager to track and drive environmental metrics. The Plant Pollution Index Coordinator is responsible for the monitoring requirement of the Pollution Prevention Index including the nature and location of the data collected on a monthly basis and reported to the corporate group in accordance with appropriate processes. The Plant Pollution Index, along with trends, is required to be discussed with plant management on a quarterly basis along with corrective actions when deviation from progress is identified through the checking and/or auditing process.
- RTO – The EHS Coordinator, as appropriate, is the Right To Operate Coordinator that is provided the authority by the Plant Manager to ensure that permits required by regulatory agencies are obtained prior to production. The Right To Operate Coordinator is responsible for review of proposed and pending legislation that may affect the plant. The Right To Operate will be updated quarterly and communicated by the corporate group by appropriate methods or data base. The Right to Operate is required to be discussed with plant management on a quarterly basis along with corrective actions when deviation from of permit attainment is identified through the checking and/or auditing process.
- PTO – The EHS Coordinator, as appropriate, is the Permit to Operate Coordinator that is provided the authority by the Plant Manager to ensure permit compliance. The Permit to Operate coordinator is responsible for developing complete inventory of all emissions and ensure permit compliance. Permit Compliance is required to be discussed with plant management on a quarterly basis along with corrective actions when deviation from compliance is identified through the checking and/or auditing process.
- Emergency – The EHS Coordinator, as appropriate, is the Emergency Coordinator that is provided the authority by the Plant Manger to track and drive environmental metrics. The Emergency Coordinator is responsible for developing and implementing a structured method for applicability of individual Emergency Scenarios around the site’s emergency conditions. The Emergency Planning, along with emergency drills is required to be discussed with plant management on a quarterly basis along with corrective actions when deviation from progress is identified through the checking and/or auditing process.
Required Experience
REQUIRED QUALIFICATIONS:
- Four (4) year degree in occupational safety, industrial hygiene, environmental discipline or equivalent.
- 5-7 years of experience with an emphasis in environmental, health and safety program management and employee training.
- PREFERRED QUALIFICATIONS:
- 7-10 years of experience preferred
- Experience managing a team and developing staff
- Ability to demonstrate managerial courage (e.g., managing varied interests representing potential conflicts)
- Advanced degree desired
- Comprehension of Tenneco, industry, state, and country EHS requirements.
- Strong ability to leverage data to make/gather support for business decisions
- Strong team-building skills
- Strong organizational skills
- Adept at utilization of company-wide system for reporting EHS data and information
- Professional certification (recommended) (Certified Safety Professional, Certified Industrial Hygienist, Certified Hazardous Materials Manager, or country equivalent where available).
We are committed to the safety and health of our employees. We adhere to social distancing recommendations and other protocols, ensuring a safe work environment for all.