PROCESSING APPLICATION
Hold tight! We’re comparing your resume to the job requirements…
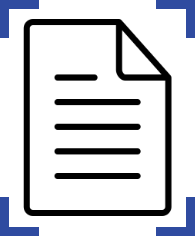
ARE YOU SURE YOU WANT TO APPLY TO THIS JOB?
Based on your Resume, it doesn't look like you meet the requirements from the employer. You can still apply if you think you’re a fit.
Job Requirements of Snr Quality Engineer:
-
Employment Type:
Full-Time
-
Education:
4 Year Degree
-
Location:
Cotia, State of São Paulo (Onsite)
Do you meet the requirements for this job?
Snr Quality Engineer
- Position Tittle
- Snr Quality Engineer
- Location: Brasil - Cotia
- Responsibilities
- Supports cross-functional launch teams by design/risk evaluations and technical supplier review meetings to assure form, fit, and function of product/assembly design intent. Leads the quality aspect for the APQP/NPI process and deliverables from kick-off through successful launch containment for assigned suppliers/project.
- Strong understanding of quality, automotive, and environmental standards (e.g., ISO-9001, ISO-14001, IATF-16949, VDA 6.3, etc.). Relevant experience in Six Sigma and other problem-solving methodologies and AIAG processes.
- Support problem resolution in High Impact & Severity Quality incidents using Effective Problem-Solving process. Facilitates timely implementation of permanent corrective action and resolution for supplier related issues. Mentor suppliers on various problem-solving methodology (EPS, 5Why's, Is is-not, etc.) and launch processes (e.g., APQP, PPAP, NPI, Feasibility Study). Organize and track issues to ensure or improve timely progress on supplier deliverables. Lead problem solving, root cause analysis and skill development at suppliers using continuous improvement methodologies including Design of Experiments, AIAG EPS, FMEAs and Control Plans.
- Implements the global purchasing supplier development strategies, establishes policies / procedures and initiatives to help improve the global supply base.
- Actively participates in sourcing decision-making reviews with Sourcing Teams.
- Supports on-site supplier development to help suppliers improve their processes and achieve productivity and quality performance goals.
- Drive targets for supplier key metric performance throughout the organization.
- Create and use of spreadsheets, databases, and presentations to interpret, report and communicate information.
- Conducts supplier audits when required to improve Tenneco's supply base to drive quality and productivity improvements at existing suppliers. Audit suppliers for conformance to quality requirements and identify opportunities and weaknesses in processes, delivery, and requirements. Develop and implement corrective actions. Utilizes standard supplier assessment and evaluation tools.
- Supports global purchasing needs during supplier transitions, commodity and application teams for resourcing and new supplier launches.
- Supports major internal and new customer projects initiated by Tenneco globally.
- Implements the global purchasing supplier development strategies.
- Prepare and present supplier performance data to management level.
- Commit, when required, to foreign and domestic travel up to 50% of working time.
- Each employee has the authority to initiate action to prevent a violation of the Tenneco Integrity Policy.
- All employees will abide by their location’s EH&S policy endorsed by the local management, comply with the legal and other requirements and operational controls established under its EHSMS, work toward achieving established objectives and targets, and conform to procedures consistent with the ISO 14001 standard. An employee should report, and if necessary, stop, any activity that does not conform to the policy or may injure himself/herself.
- Education
- Bachelor’s degree in science or engineering or equivalent experience.
- Experience
- 3+ years’ experience working in a quality, engineering, procurement, or engineering role. Manufacturing experience preferred.
- Excellent interpersonal skills, especially communications skills (oral and written) and the ability to influence the behavior of peers and others outside the direct reporting line.
- Experience performing internal or external audits. Certified QMS (IATF or ISO) Lead Auditor preferred.
- Related Business or Technical discipline experience (e.g., steel, stamping, forging, machining, casting, cold heading, rubber, plastic, heat treating, motors, pumps, sensors, PCB, filters, pressure sensors, Heater blankets, controllers, pump & motor assemblies, and electromechanical products).
- APQP, PFMEA, MSA, Control Plan, Process Capability, PPAP & Error proofing process training and practical experience required.
- Understands the process and tools of effective problem solving and able to lead an improvement team.
- Trained Understanding of GD&T
- Six Sigma Green Belt will be a plus.
- Creative and innovative thinking.
- Ability to initiate, lead and sustain change.
- Strong data-driven decision-making skills.
- General project management skills and experience.
- Ability to read and write English.
- Excellent Microsoft Office skills.
- Must be willing to travel internationally, as required.
- Specific proficiency levels for each job skill required are defined in the Skills Requirement Checklist for this job title.
- Skills Checklist
Employee Name
The following must be completed in its entirety.
*Level of Requirement – Indicate either Optional or Required Skill for the position.
**Source of training for each job skill may be provided by the supervisor or manager of that department, in addition to, or in place of, the primary source identified on the checklist.
*** Each row must be marked with Y or N and manager’s initials
Skill/Training
*Level of Requirement (Optional/ Required)
Source for Training
(If Known)
Proficient in Skill
Yes/No***
HR or Direct Manager’s Initial***
Creating a Respectful Workplace
Required
Human Resources
Integrity Training
Required
Human Resources
Extensive knowledge of all of the “Core Tools” (FMEA, SPC, MSA, APQP & Control Plan & PPAP)
Required
On the Job / TMS/External
Working knowledge of Design of Experiments (DOE)
Optional
External
Advanced Statistical Skills (Probability, Inference, Confidence Intervals, Hypothesis testing, Regression, ANOVA, Reliability, etc.)
Optional
External
Extensive knowledge of the 7 Basic Quality Tools (cause & effect diagram, flow chart, histograms, check sheets, pareto chart, scatter diagram and control chart)
Required
On the Job / TMS/External
Effective Problem Solving knowledge
Required
TMS
Knowledge of Basic problem solving tools (Is / Is Not and 5 Why)
Required
On the Job / TMS/External
GD&T – Geometric Dimensioning and Tolerance
Optional
External
Basic Management Principles ( Planning, Leading Delegating, Controlling, Organizing & Staffing)
Required
On the Job
Basic project management skills
Required
On the Job / TMS
Recognizing and developing processes for effective deployment of the QMS and business operations that impacts customer quality
Required
On the Job
Develop and have knowledge of the Global Supplier Quality Manual and corporate procedures
Required
On the Job
Lead Auditor, including IATF 16949 & ISO 9001
Required
External/ TMS
Knowledge of Supplier Quality Management systems
Required
On the Job
Knowledge & understanding of statutory, regulatory requirements that impact supplier/supplier management.
Required
On the Job
Ivalua Administrator
Required
On the Job
PEOD
Required
On the Job
Techline access
Required
On the Job
ETQ Reliance access
Required
On the Job
SharePoint sites
Optional
On the Job